- Employees completing this program will evaluate the effectiveness of systems and processes within your organization’s value chain.
- They will design data models and analyze results to render useful impacts on industrial and operational processes.
- Through projects, they will map systems and processes within the context of your organization’s existing state, desired state, and transitional state.
- They will communicate and employ effective change management tools to move systems and processes toward your organization’s future goals.
Explore the core coursework and certificates that stack into the Masters of Engineering in Systems Engineering and Technology Management.
- In this three-course, online graduate certificate, participants complete projects to improve processes and lead teams through the steps needed to systematically identify, quantify, and fix problems.
- They will create effective process deployment strategies and reduce the risk of mistakes and process weakness.
- Statistical methods will be deployed for Design of Experiments, Theory of Innovative Problem-Solving, and establishing Key Performance Indicators to validate recommendations.
- Those who complete the certificate will earn a Rensselaer at Work Lean Six Sigma Yellow and Green belt from Rensselaer at Work.
- In this three-course, online graduate certificate, participants will map and evaluate your value chain, including clients, your clients’ clients, and vendor implications.
- They will determine quality characteristics and performance standards for elements within your supply chain.
- Participants will identify criteria for evaluating the efficacy of a logistics pathway into and from your organization, as well as return.
- With this in hand, participants will develop plans to reduce vulnerabilities within your supply chain and recommend how to manage and improve your vendor relationships to ensure logistic and quality goals are achieved and exceeded.
See the three courses and projects completed in the Supply Chain and Logistics Certificate.
- Participants will map and critically analyze the elements in a system or process within your organization.
- Then, they will quantify performance relative to predefined criteria and established metrics.
- Within the context of their work, they will evaluate how a system’s performance is likely to change and implement actions to improve its performance.
- In the end, participants can forecast performance issues given known attributes, while making reasonable and sound assumptions to represent unknowns.
Explore the three courses and project details for the Systems Engineering Certificate.
- Participants in this 5-week, online, non-credit course develop a strategic plan for implementing smart manufacturing within their organization.
- Endorsed by CESMII – The Smart Manufacturing Institute, their acceleration framework is used to assess your organization’s current state, develop an aligned future state vision, and create a roadmap to achieve your organization’s business objectives.
- Course materials are accessed on the RensselaerStudio. Evening (ET) synchronous sessions are scheduled once a week and recorded for those unable to attend.
- The goal of the course is to prioritize high-value target areas within your organization to optimize people, processes, and technology to achieve your organization’s goals.
Build Effective Teams
We will partner with you to orchestrate upskilling your intradepartmental teams or employees across business units to escalate the achievement of your organizational goals. Shared learning experiences build a sense of community and collaboration, align approaches and tools company-wide, reduce waste, and improve the completion of work and resource spend.
Within a month, participants will gain insight of the real challenges, gaps and opportunities and then develop a plan to attack.
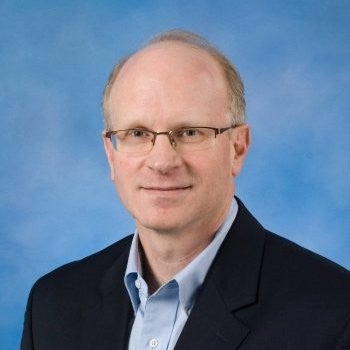